Machinery & Equipment
According to APO Research, total revenue for industrial rotary encoders is expected to reach nearly $3.08 billion by 2031
23 April 2025
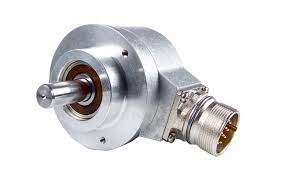
The global industrial rotary encoder market has demonstrated steady and resilient growth from 2020 to 2024, underpinned by the accelerating adoption of automation across diverse industrial verticals. Despite a moderation in growth during 2024 due to broader economic uncertainties and a cyclical downturn in the automation sector, the overall market expanded at a compound annual growth rate (CAGR) of 4.04% in volume and 5.52% in value. This growth trajectory was particularly buoyed by high-performance demand from sectors such as machine tools, industrial robotics, mining and metal processing, and off-highway machinery, where the requirement for precise motion control and reliable feedback mechanisms remains critical.
According to statistics and forecasts from APO Research, During the 2020–2024 period, global shipments increased from 9.13 million to 10.70 million units, while market revenue rose from USD 1.52 billion to USD 1.89 billion. This positive momentum reflects not only the expanding base of automation assets worldwide but also the transition toward higher-specification encoders. Customers are increasingly favoring models with enhanced ingress protection (IP67/69K), high resolution, digital communication interfaces (e.g., PROFINET, EtherCAT, SSI), and robust mechanical durability suited to demanding industrial conditions.
A closer look at the application landscape in 2024 reveals a relatively balanced distribution of demand across critical sectors. Machine tools (18.7%), material handling (13.8%), industrial robotics (13.4%), and off-highway equipment (12.1%) accounted for the majority of encoder usage, reflecting their central roles in automated production and mobile equipment control. At the same time, specialized sectors such as mining and metal processing (12.7%), fluid machinery (8.1%), and pulp & paper (5.9%) continue to present strong application-specific demand for ruggedized encoder solutions. Railway automation (5.6%), agriculture (4.0%), and packaging machinery (3.0%) also contribute to market diversity, with growth driven by infrastructure investment, productivity upgrades, and regional digitization efforts.
Regionally, Europe remains the largest manufacturing hub, producing 3.99 million units in 2024, supported by Germany, Italy, and France’s leadership in machine tools, automation, and transport systems. Asia-Pacific has emerged as a high-growth region, propelled by China’s thriving robotics sector, Japan’s precision engineering ecosystem, and India’s expanding industrial base. North America, led by the U.S., continues to represent a technologically mature market, with significant adoption in fluid control, packaging, and mobile equipment. The rest of the world, notably Latin America and parts of Eastern Europe and the Middle East, is gaining momentum—particularly in heavy industries such as mining, metals, and infrastructure-linked equipment.
According to APO Research,, the industrial rotary encoder market is projected to maintain an accelerated expansion phase, with forecasted unit sales reaching 16.02 million and total revenue approaching USD 3.08 billion by 2031. The anticipated CAGR for 2025–2031 stands at 6.55% in volume and 7.02% in revenue, driven by continued automation adoption, technological innovation, and penetration into emerging markets. Average unit prices are expected to stabilize around USD 169.8, reflecting the dual impact of increased product standardization and manufacturing efficiency gains, offset by incremental adoption of higher-value encoder configurations.
As encoder technology becomes more standardized, especially in basic incremental types, manufacturers face intense pricing competition, particularly from lower-cost Asian vendors. This challenges profit margins and discourages innovation at the low end of the market.
In industries like pulp & paper, mining, and fluid machinery, rotary encoders face issues related to ingress of dust, slurry, moisture, and oil, requiring high IP-rated encoders with protective housings. Failures in such environments can lead to costly downtimes and frequent replacement cycles.
Optical encoders rely on precision glass disks, rare-earth magnets, and specialized semiconductors. Geopolitical disruptions or shortages (e.g., in rare earths or optical photodetectors) can impact production lead times and costs.
Many industrial systems still operate with legacy PLCs or proprietary control protocols. Integrating modern encoders with digital interfaces often requires middleware or custom firmware, increasing system complexity and hindering adoption in certain retrofit applications.
While open protocols like SSI and BiSS are gaining traction, many high-performance encoder systems still rely on proprietary communication protocols. This creates vendor lock-in and limits interoperability across platforms.